Are you searching for a machine vision partner for your automation or custom instrument or application? Do you need a company that actually understands inspection? Unlike standard integrators, our company offers a wide breadth of knowledge in metrology and inline inspection.
First and foremost, IST Precision understands inspection and metrology. Our roots extend back over 20 years to the Center for Precision Metrology at UNC Charlotte, a premier educational institution dedicated to metrology—the science of measurement. Their rigorous program branches into a variety of fields, from optical metrology and measurement uncertainty to custom instrumentation development. Over the years, IST Precision has amassed experience in both inline vision inspection and custom stand-alone inspection equipment. In this short article, we will discuss the use of cameras and high-resolution monitors for quality control manual inspection.
Leveraging Vision and 8k Monitors
In one application, a client approached us with a problem: their operators needed to distinguish very tiny features (under 50 micrometers) over a large viewing field of 110 x 55 mm in a lab environment. There are many fields where this need arises from high density electronic inspection to thin film defect inspection to medical diagnostics. To put this in perspective, 50 micrometers is approximately the width of a human hair and right at the limit of the lower visibility limit of the human eye; attempting to find such a tiny feature in a large area (2 x 4 inches) can be exceptionally difficult and strain operators’ eyes, FIGURE 1 and 2.
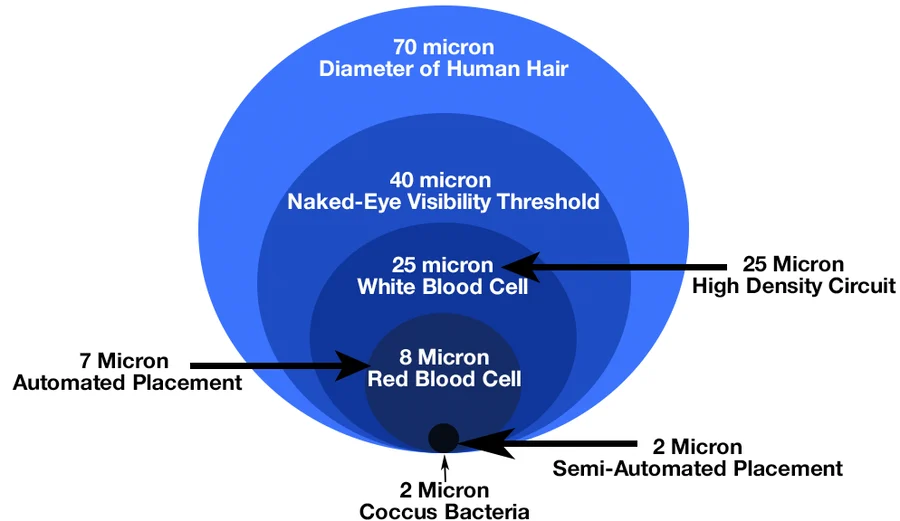

FIGURE 1 – Illustrations showing size comparisons of human hair, white blood cells and red blood cells
Images taken from:
https://www.bench.com/setting-the-benchmark/how-big-is-a-micron
https://hotflusher.com/How-Big-is-a-Micron
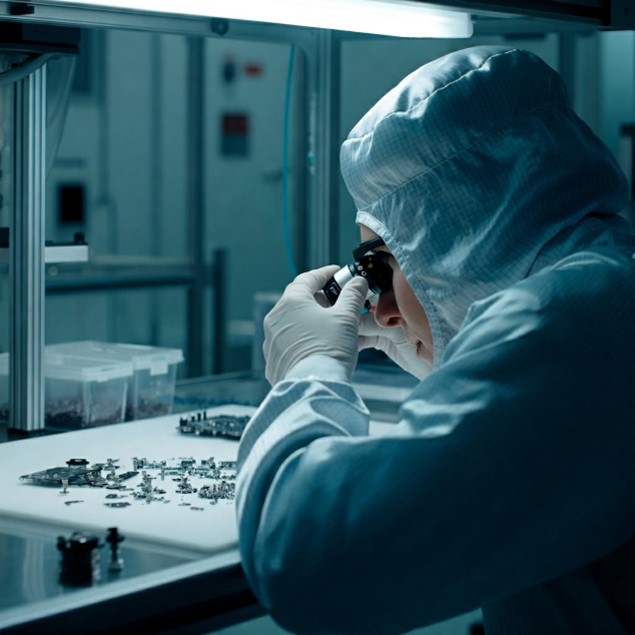
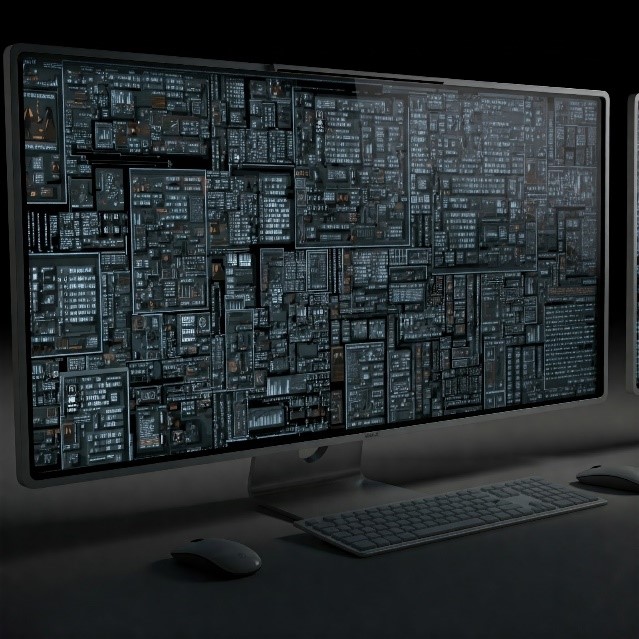
FIGURE 2 – Straining to see features and illustration displaying high resolution image on a large monitor
Our approach was a dual-camera solution combined with an ultra-high-resolution monitor, see Figure 3. We wanted the operator to distinguish small features on a high-resolution monitor rather than straining to see them directly on the product. After careful review, we recognized that both the monitor and cameras played a critical role. If the cameras were high resolution but the monitor was low resolution, the human eye’s ability to discern detail would be compromised.
The monitor we used was an 8K monitor with a resolution of 7680 x 4320. These high-resolution monitors are commonly used in the medical field (e.g., radiology) to improve the accuracy of human diagnostics. Our goal was to ensure that the monitor quality closely matched our cameras so the human eye could distinguish small defects in the product material displayed on the monitor.
Next, we used two 24 MP (mega pixel) cameras, each having 5328 x 4608 pixels. The reader will notice that one camera is nearly at the resolution of an 8K monitor. Ideally, we would have preferred a higher resolution monitor, but at the time of this project, an 8K monitor was about as high resolution as we could get.
The figure below shows our device’s test stand, which has two cameras with high-resolution optics. The fixture below uses a glass surface with a backlight for better viewing. The backlight intensity is adjustable using a thumbscrew. All the parts were machined in IST’s machine shop.
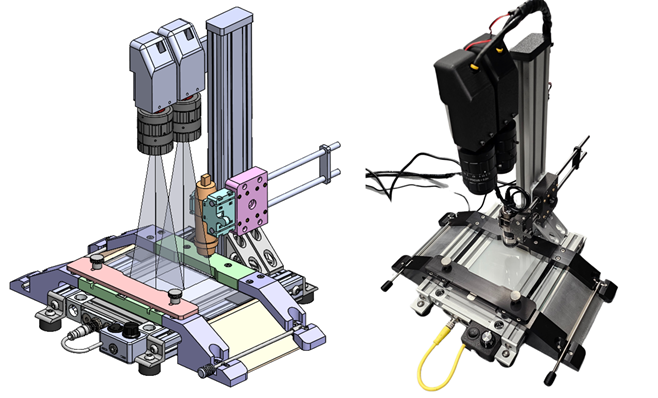
The dual cameras were fed over GigE to a video graphics card on a computer workstation. We integrated this into a custom python user interface and developed code to blend the two images together seamlessly, so on the screen it appears as a single image, figure 4 and 5. Our code also included zoom functionality, and ultimately, we were able to achieve a frame rate of about 16 frames per second—sufficient for the application while still enabling the operators to see high-resolution images on the 8K monitor. The user interface code also integrated a third camera, a USB microscope from Dino-Lite. This allowed the operator to switch between the two main cameras or the microscope camera for much closer viewing of a small field of view.
This was a great project for IST’s vision and optics group, and we look forward to more in this area for our clients.
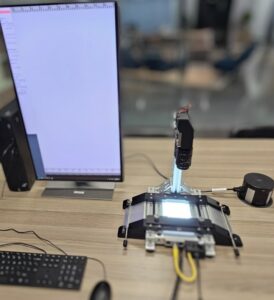
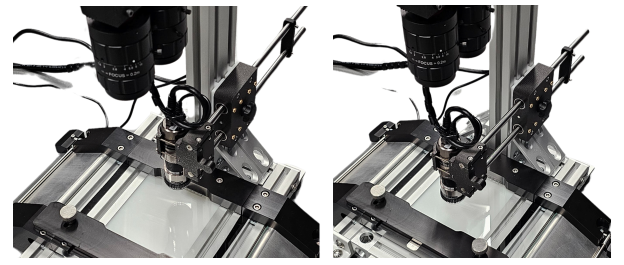